Are you curious about screen printing and wondering how to use it for your next project? You’re in the right place! Whether you’re new to this method or looking for tips to perfect your process, this guide covers everything: what screen printing is, where it shines, its pros and cons, and practical tips for success.
What Is Screen Printing?
Screen printing, often called silk screening, is one of the most popular POD methods in the world today. This technique uses a mesh screen to transfer ink onto a surface, such as fabric, paper, or plastic. It is very popular, especially for printing on articles such as t-shirts and almost any other apparel, posters, and even some placards or signs.
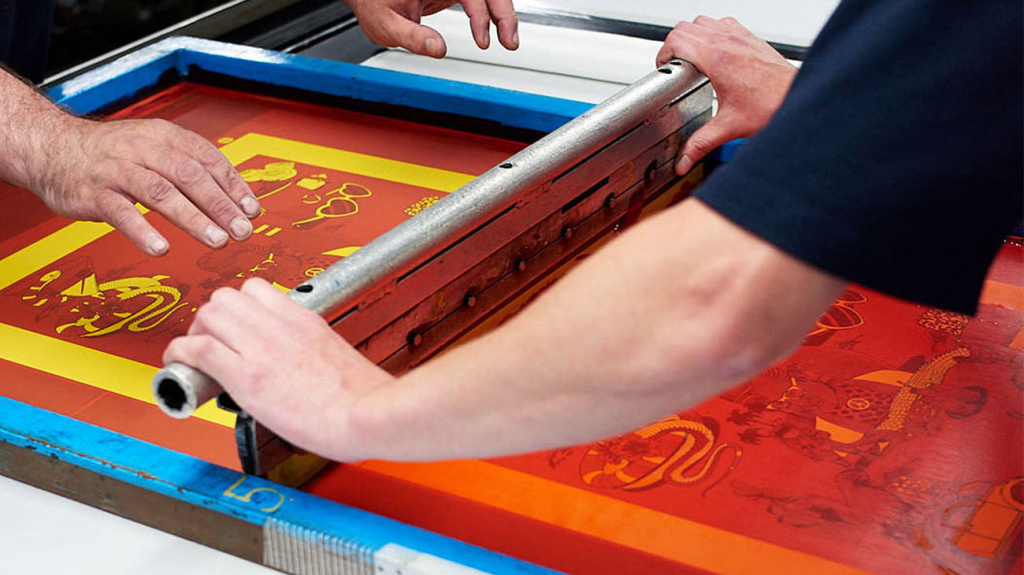
The printing process involves creating a stencil (or screen) for each color in your design. Then, the ink is pushed through the mesh using a squeegee, ensuring vibrant and durable prints. One of the best things about screen printing is its versatility, allowing it to handle both small and large batches of prints efficiently.
How Does Screen Printing Work?
The screen printing process might seem a little complicated at first, but it becomes clear when you understand the steps. Now I will give you an explanation of how it works:
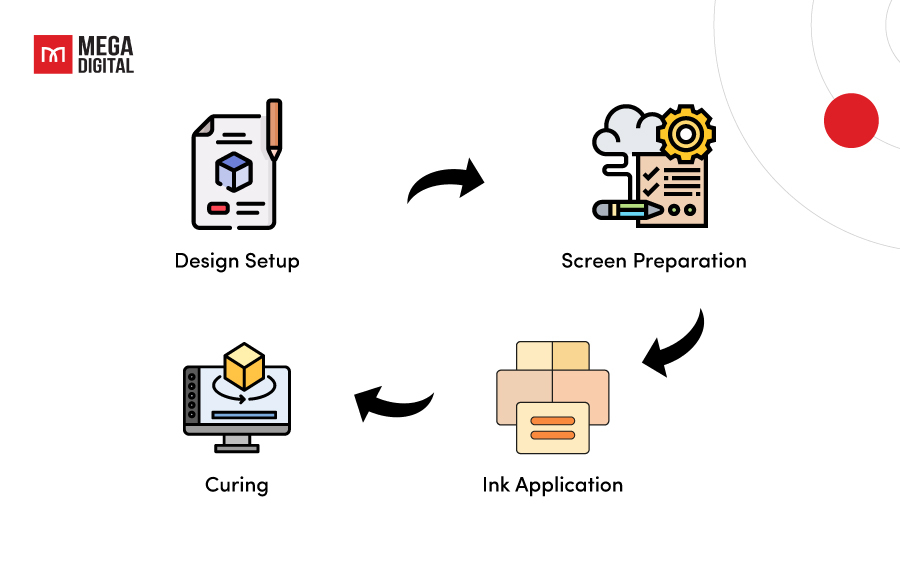
- Design Setup: First, you separate your design by colors, assigning each color to its own screen or stencil.
- Screen Preparation: Next, you coat a fine mesh screen with a light-sensitive emulsion. Then, you expose the screen to light with your design placed on top. This process hardens the emulsion in some areas, leaving others open for the ink to pass through.
- Ink Application: In this step, you place your fabric under the screen and use a squeegee to push the ink through the mesh. This transfers the design onto the fabric. For multi-color designs, you align each screen carefully to make sure everything lines up perfectly.
- Curing: Finally, you heat the printed fabric to cure the ink, ensuring it bonds with the material and lasts longer.
Screen Printing: Pros And Cons
Screen printing, like any method, has its own pros and cons. Here, I’ll go over its advantages and disadvantages to help you decide if it’s suitable for your project.
Pros
Screen printing has a set of strengths that make it a favorite of many professionals and hobbyists alike such as:
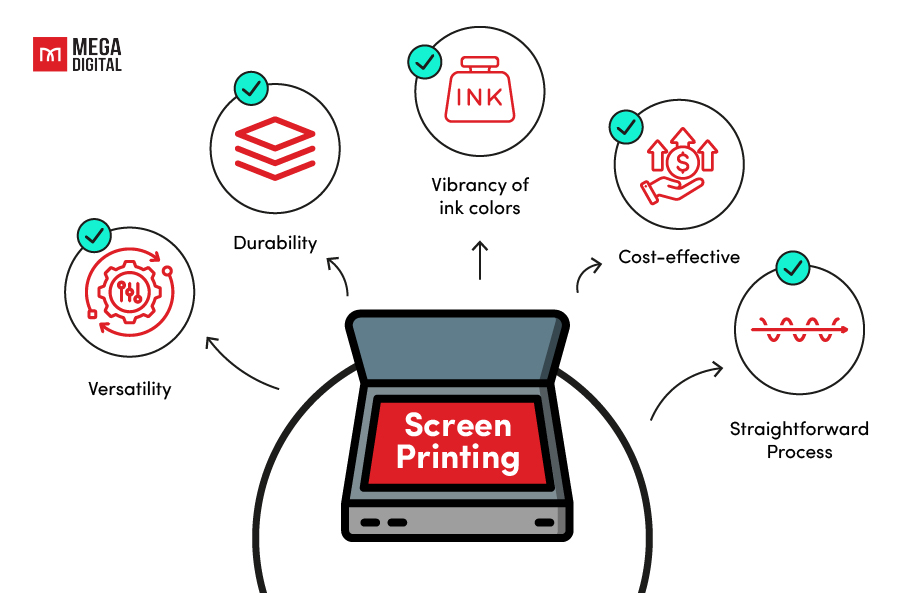
- Versatility: You can print on various materials like fabric, paper, and promotional items. This flexibility allows you to create detailed, vibrant designs on almost any surface.
- Durability: The ink bonds strongly with the material, so your prints stay intact, even through washing or exposure to the elements. This makes screen printing ideal for designs that need to last.
- Vibrancy of ink colors: Screen printing uses thick, opaque inks, which means your prints will have a bold, eye-catching finish. This makes it especially effective for designs that need to pop, especially when printed on darker fabrics or surfaces.
- Cost-effective: While setting up each screen takes some time and investment, once it’s done, printing additional items becomes cheaper. This makes it perfect for large print runs without breaking the budget.
- Straightforward Process: Though screen printing involves several steps, the process is simple and easy to follow once you get the hang of it.
Its versatility allows for printing on various materials like fabric, paper, and even promotional items, enabling the creation of vibrant and detailed designs on almost any surface. The durability of the prints is another key benefit, as the ink strongly bonds with the material, ensuring longevity even through frequent washing or exposure to harsh elements.
>>> Read more: Screen Printing vs Heat Press: What Works Best for Your Projects?
Cons
Yet, screen printing does have its downsides. Below are some significant limitations you should keep in mind:
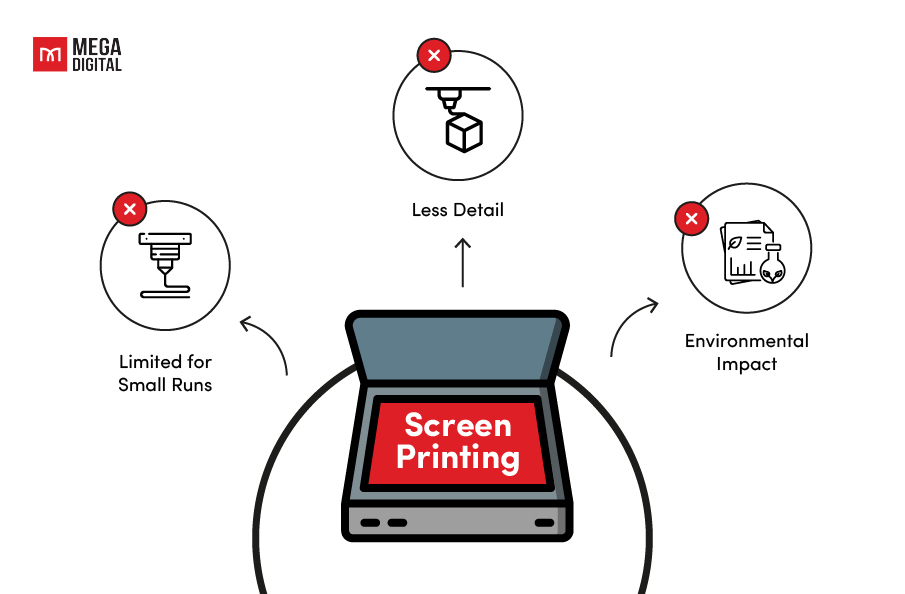
- Limited for Small Runs: Due to the set-up procedure involved in preparing screens for each color, low quantities using screen printing will be costly and time-consuming. Therefore, if you’re printing just a few pieces, this method might not be the most practical option.
- Less Detail: Screen printing isn’t ideal for designs with complex details or thin lines. The screen’s mesh restricts how much detail can be achieved, so if your design needs fine, detailed work, methods like digital printing might be more suitable.
- Environmental Impact: This method can affect the environment, especially because of the chemicals in the making and cleaning process. Even though there are environmentally friendly inks and methods, the process can still create waste and pollution if it is not managed correctly.
6 Main Types of Screen Printing
Screen printing doesn’t follow a single approach, so depending on your design and project needs, there are some techniques that can help you gain specific results. Now, let’s dive into the six main types of screen printing and get to know how each works.
#1 Spot Colour Screen Printing
First, we have spot color screen printing. This is the most common type of screen printing that uses solid, opaque colors, applied individually through separate screens. This method is quite simple and reliable, guaranteeing vibrant and consistent results for your designs with a limited color palette.
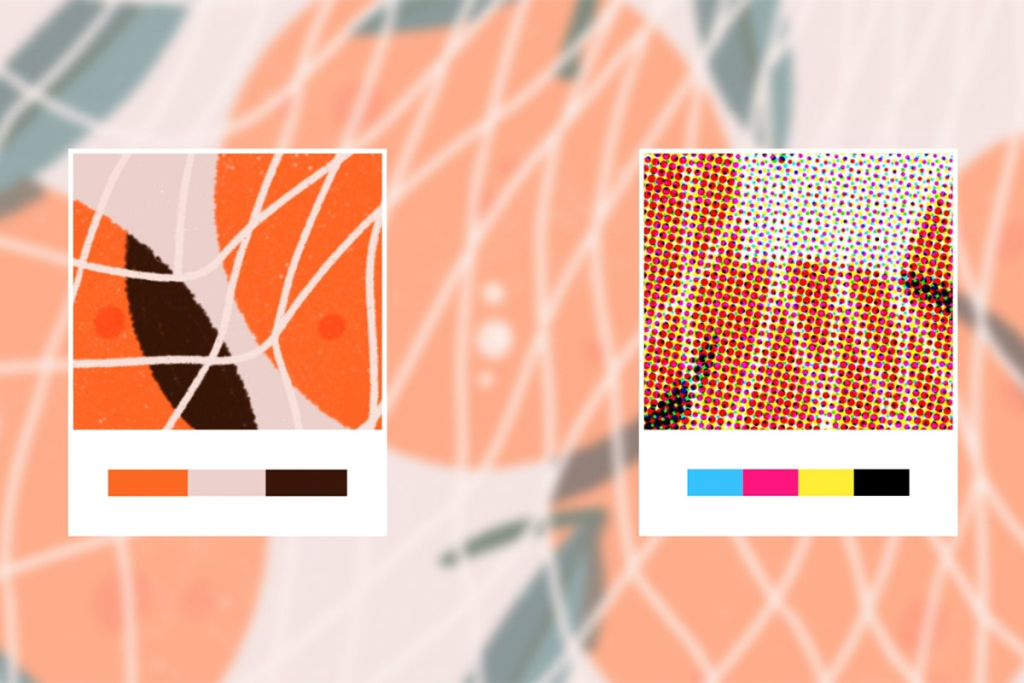
Additionally, spot color screen printing works best at delivering solid, vivid colors, making it an excellent choice for designs that don’t use many colors. It’s also particularly effective when color accuracy and strong rich shades are crucial to the project.
#2 Halftone Printing
Halftone printing is simply making a lot out of little. It uses different point sizes and positions to create a smooth tint or shading in the design and is different from spot color printing since it only uses one ink color.
And the result? A design with depth and dimension, perfect for capturing gradients or a photographic effect.
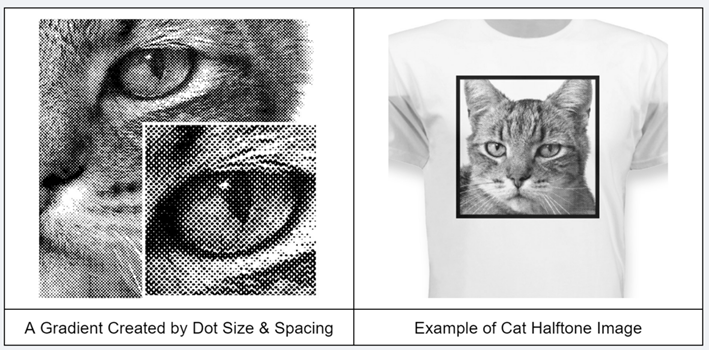
Halftone printing is ideal when you want to add subtle shading without complicating the process. For example, if you’re designing a single-color poster or apparel piece with a vintage vibe, this method delivers an amazing yet cost-effective result.
#3 Grayscale Printing
Grayscale printing is your go-to method when detail is everything. It focuses on using varying shades of gray to capture intricate details and textures. This method uses different shades of gray to capture fine details and textures. By transforming a color image to grayscale, the design keeps its depth and richness through differences in light and dark areas.

This approach works well for black-and-white designs that need fine details, as it can reproduce textures and gradients without using multiple colors.
Furthermore, grayscale printing offers a budget-friendly way to create detailed designs that focus on contrast and texture instead of color. It’s a great option if you want your design to have a polished timeless look.
>>> Read more: Sublimation vs Screen Printing: Which One is Right for You?
#4 Duotone Printing
On the other hand, duotone printing is where creativity meets simplicity. This method uses two contrasting ink colors to add depth and dimension to your design. By blending these two inks, it creates a dramatic contrast between light and shadow, resulting in more dynamic, artistic, and undeniably eye-catching products.
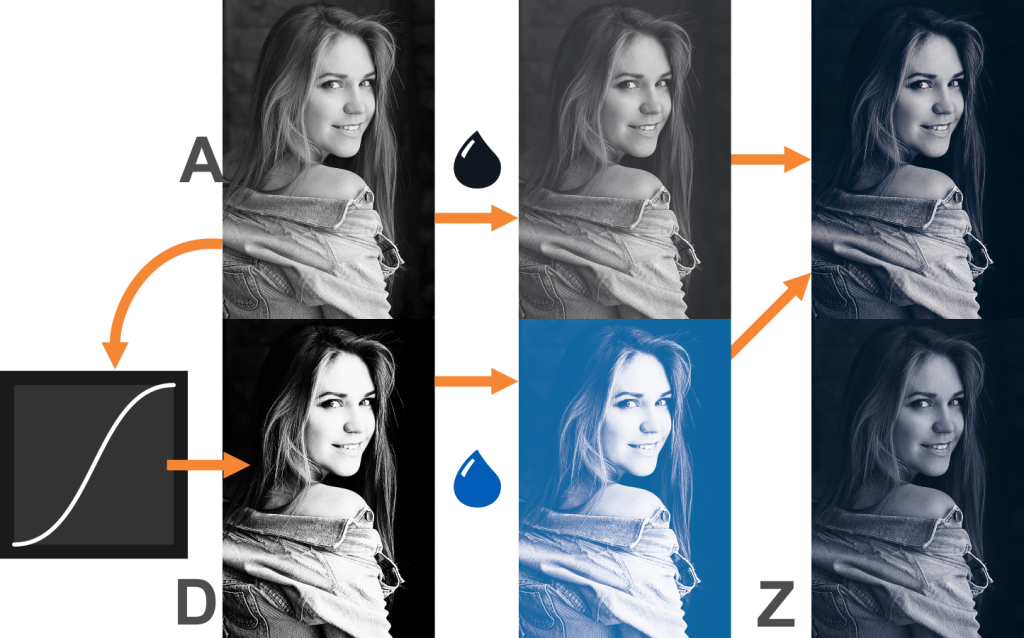
Two-color printing offers a smart and budget-friendly option compared to using all colors when you aim to create a certain vibe or look. This technique is well-suited for designs that call for a layer of artistic flair and impact, making it a versatile choice when you want to achieve both creativity and simplicity with just two colors.
For example, if you want to evoke a specific mood or give your design a retro edge, duotone printing is a fantastic option. It’s particularly effective for marketing materials or album covers where a bold aesthetic makes all the difference.
#5 CMYK (4-Color Printing)
I bet CMYK printing will be your go-to method for full-color designs. It uses four ink colors including cyan, magenta, yellow, and black to create a wide spectrum of hues. By carefully layering these inks in tiny, precise patterns, CMYK printing makes it possible to produce stunning, high-quality visuals like photographs and detailed illustrations.
While CMYK can get a lot of colors, you still need to attend carefully to ensure proper color registration.
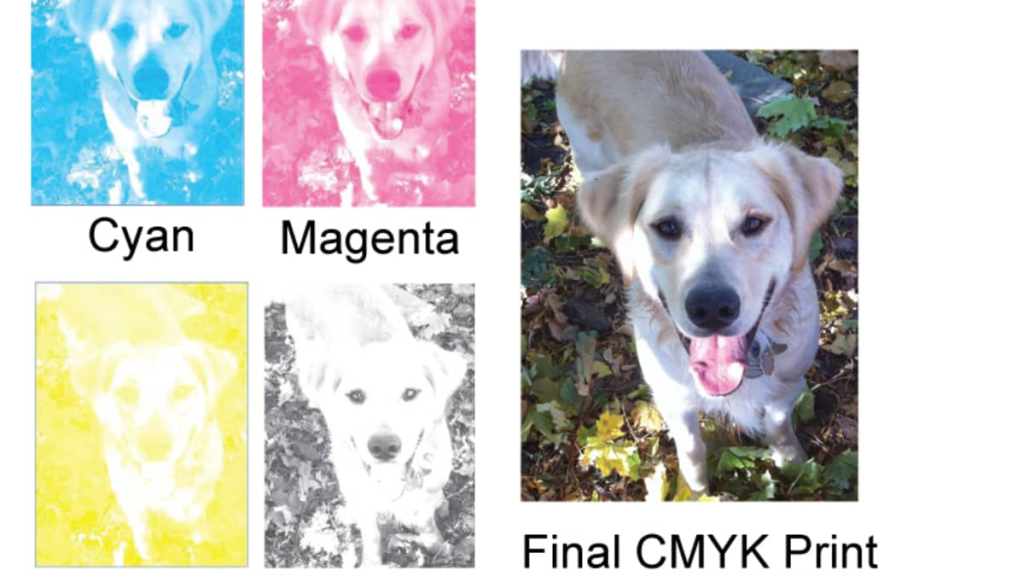
Another benefit of CMYK printing is that it can create photorealistic designs and accurate color blending, which is ideal for projects that have lots of colors and detailed pictures. However, it may be less efficient for designs with fewer colors or simple graphics.
#6 Simulated Process Printing
Last but not least, simulated process printing combines multiple spot colors to simulate the effect of full-color printing. This method is particularly useful for dark fabrics or materials that standard CMYK printing might have trouble with.
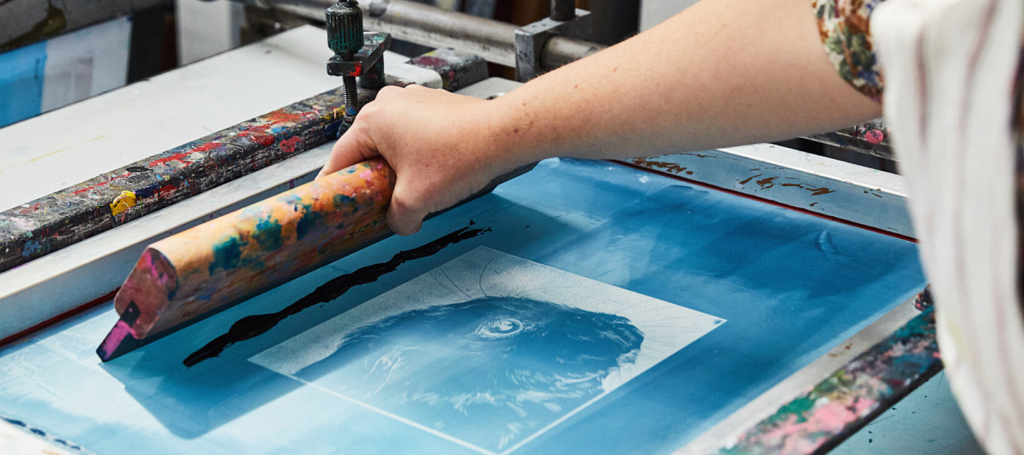
Simulated process printing can produce bright, detailed designs even on non-white surfaces by mixing different spot inks.
What makes simulated process printing stand out is its ability to produce vivid, lifelike images without the high costs and complexity of traditional CMYK printing. This method is particularly great for designs that need bold, attention-grabbing prints, especially when printing on dark-colored garments or promotional items.
Best Fabrics for Screen Printing
The fabric you choose for screen printing plays a crucial role in the final result of your design. Some materials work better than others due to their texture, absorbency, and durability. Below, we’ll explore the best fabrics for screen printing and why they’re ideal for this method.
Cotton
Cotton is a screen-printing superstar. Its smooth texture and high absorbency allow for vibrant, detailed prints that really stand out. Plus, it’s soft and comfy – perfect for t-shirts and everyday wear.
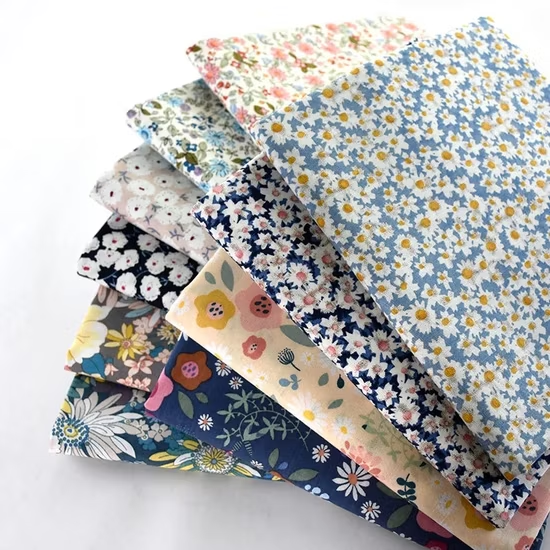
Another great thing about cotton is its durability. It holds up well after washing, making sure your designs last.
However, you still need to keep an eye on the thickness—thicker cotton can sometimes make prints look less sharp, so go for a balanced weight for the best results.
Polyester
Are you looking for a fabric that’s tough, long-lasting, and resistant to fading? Polyester has you covered. Its smooth texture is perfect for creating sharp, high-quality prints, making it a favorite for sportswear and activewear. Plus, its moisture-wicking properties keep you dry and comfortable during any activity.
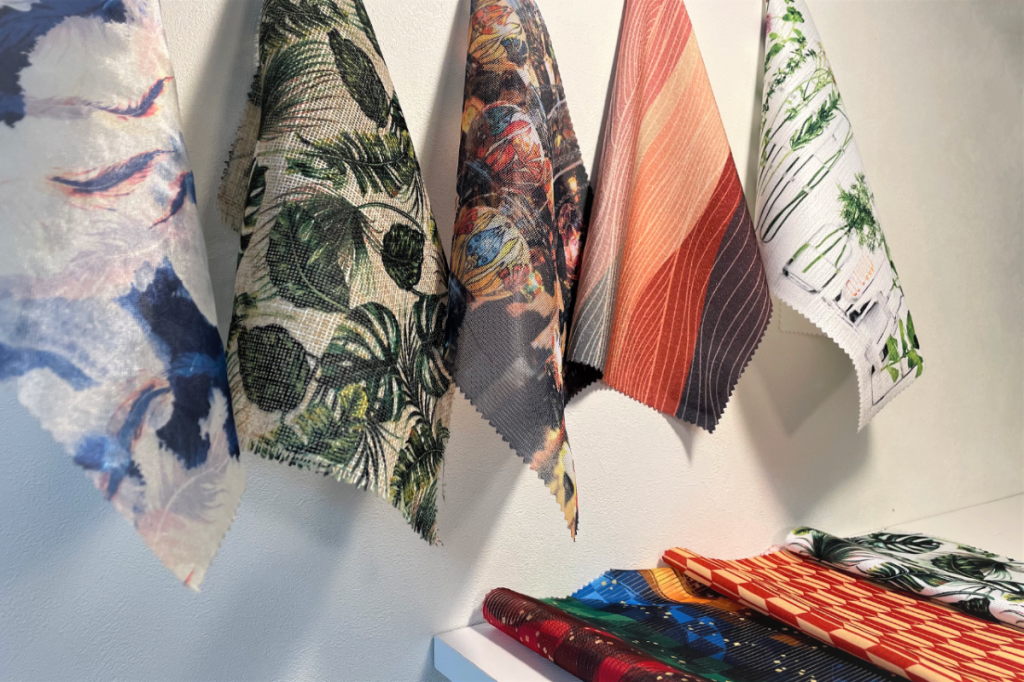
However, polyester does come with its quirks. It’s trickier to print on than cotton, but don’t worry! Modern techniques and inks like plastisol have made the process much simpler. You just need to keep in mind that polyester needs special inks and precise temperature settings to get the best results.
Cotton-Polyester Blends
Can’t decide between cotton and polyester? Cotton-poly blends give you the best of both. You will get the softness and easy printability of cotton combined with the durability and wrinkle resistance of polyester.
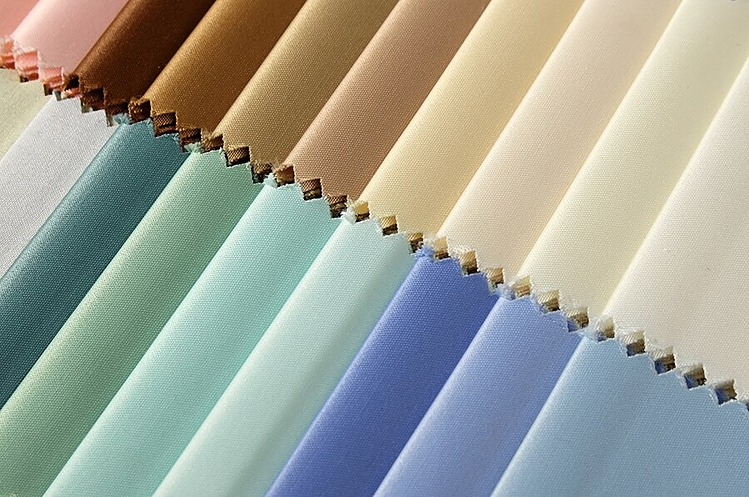
They absorb ink well and provide a smooth surface for clear designs. Plus, they last longer than pure cotton, making them a practical and budget-friendly option.
Silk
For something more exclusive, silk brings a touch of luxury. Its smooth texture allows for intricate, high-quality prints, making it a favorite for premium products like scarves or designer apparel.
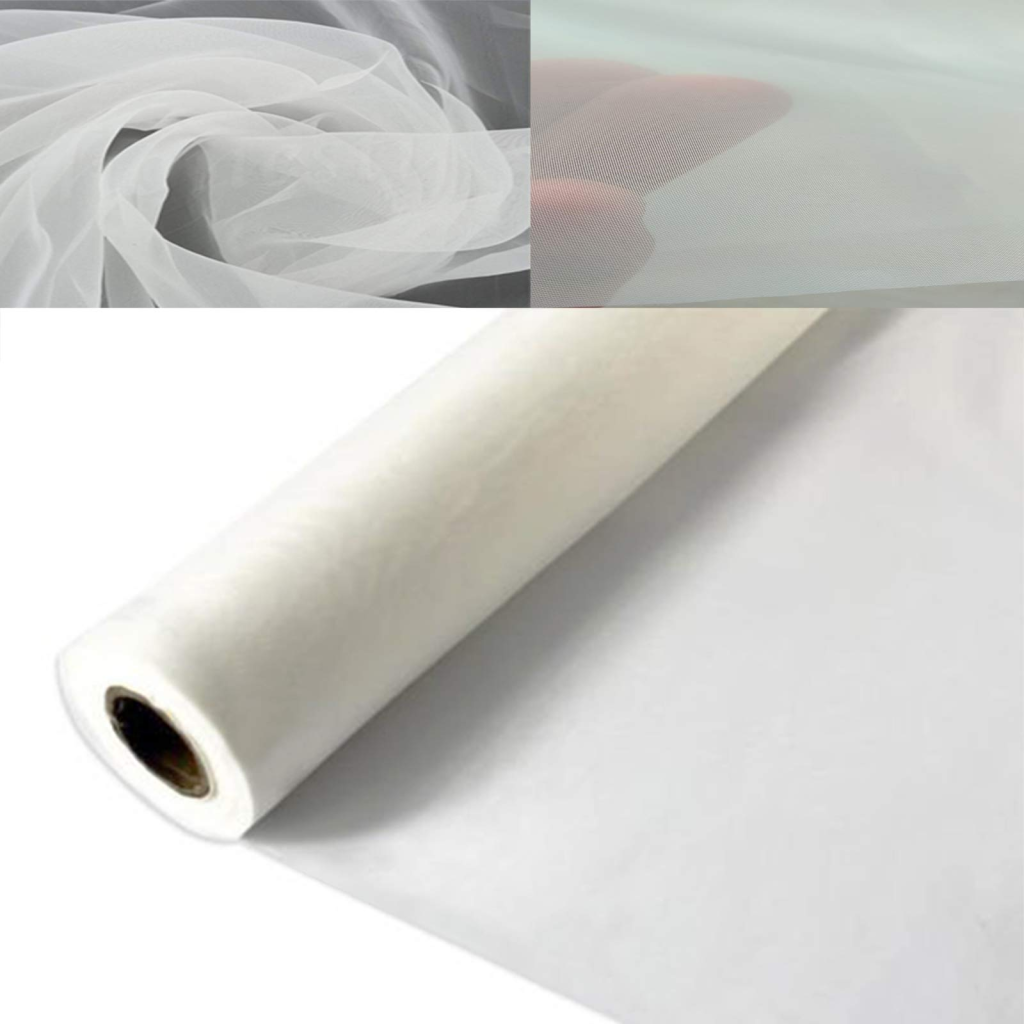
However, you also need to remember that silk is more delicate than other materials, so it requires more care during printing. It also tends to be more expensive, making it less ideal for bulk printing projects but a great choice for unique, high-end prints such as custom designer clothing, luxury home textiles, or exclusive fashion accessories.
Linen
If you’re going for a natural, textured look, linen is your fabric. Its open weave gives designs a rustic or vintage feel, making it a favorite for eco-friendly brands or artisanal products.
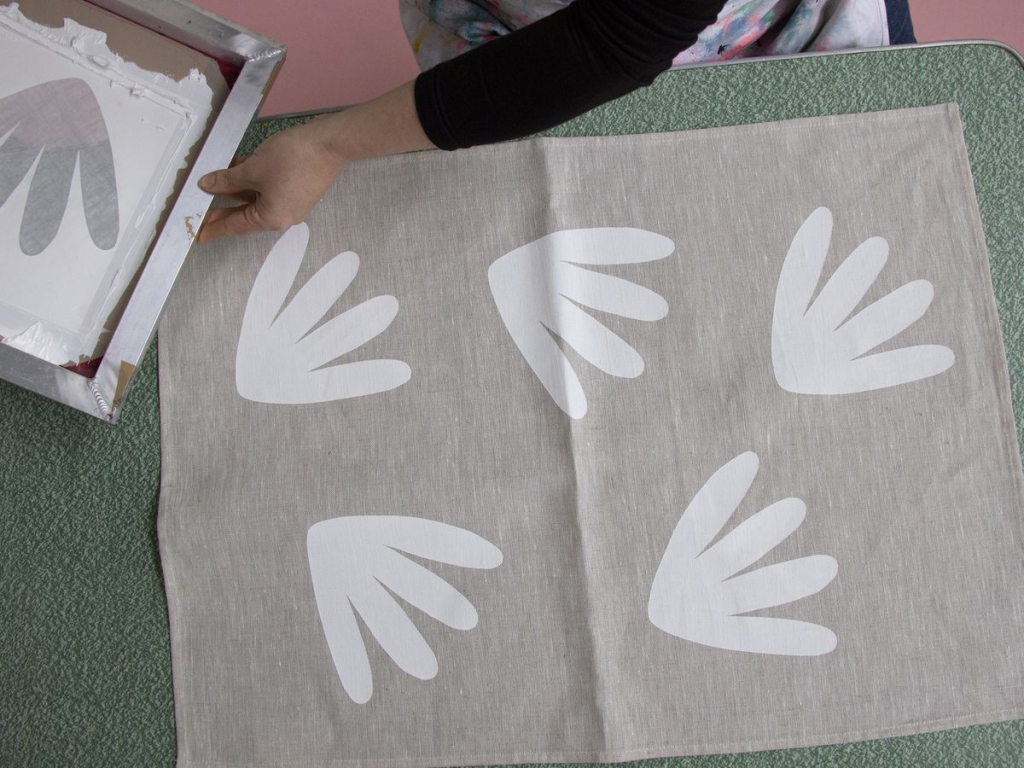
Linen soaks up ink beautifully, ensuring durable prints. However, its coarse texture can make precision tricky. This fabric shines when you’re aiming for an organic, handmade vibe—perfect for rustic home goods or relaxed apparel.
Canvas
Need something tough? Then you must take a look at canvas. Its heavyweight and tight weave makes it perfect for tote bags, banners, and even upholstery. Plus, it holds ink exceptionally well, ensuring vibrant designs that stand up to daily wear and tear.
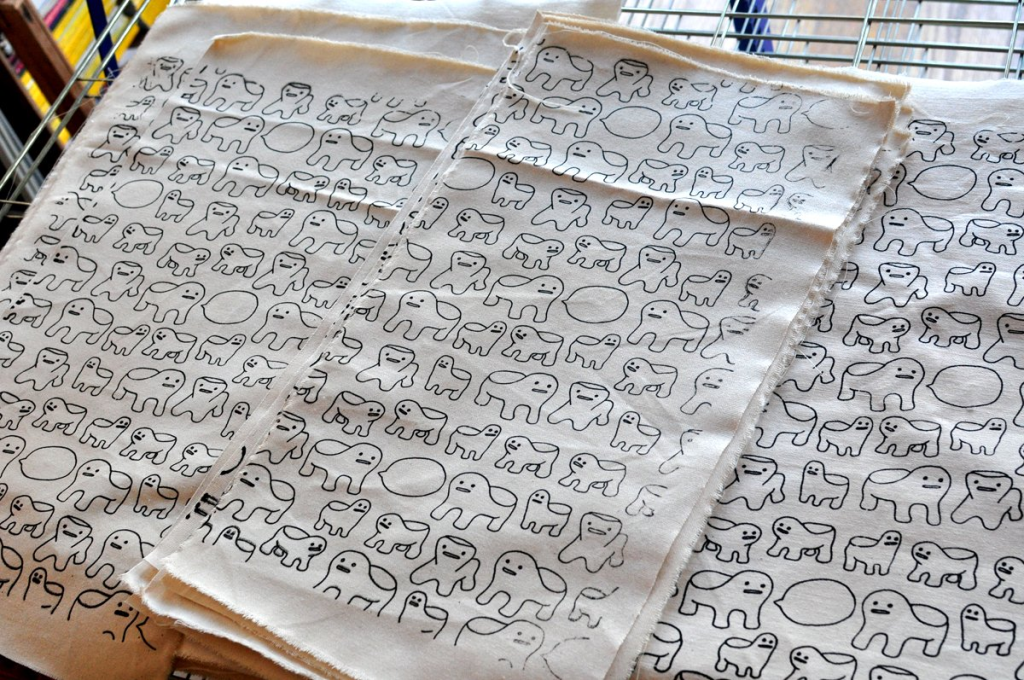
However, because of its thickness, canvas is less flexible than lighter fabrics, so it’s best suited for items that don’t require much movement or stretch.
Tips for Successful Screen Printing
Want your screen prints to pop and last? It’s not just about knowing the process – it’s about nailing the little details. Let me walk you through some essential tips that will make your screen printing projects stand out.
Choose the Right Ink
The ink you choose can make all the difference.
Take plastisol ink, for example – it’s a classic go-to for t-shirts. Why? It stays on the surface of the fabric, giving you vibrant, bold colors that last. Perfect for designs that need to pop and stay sharp.
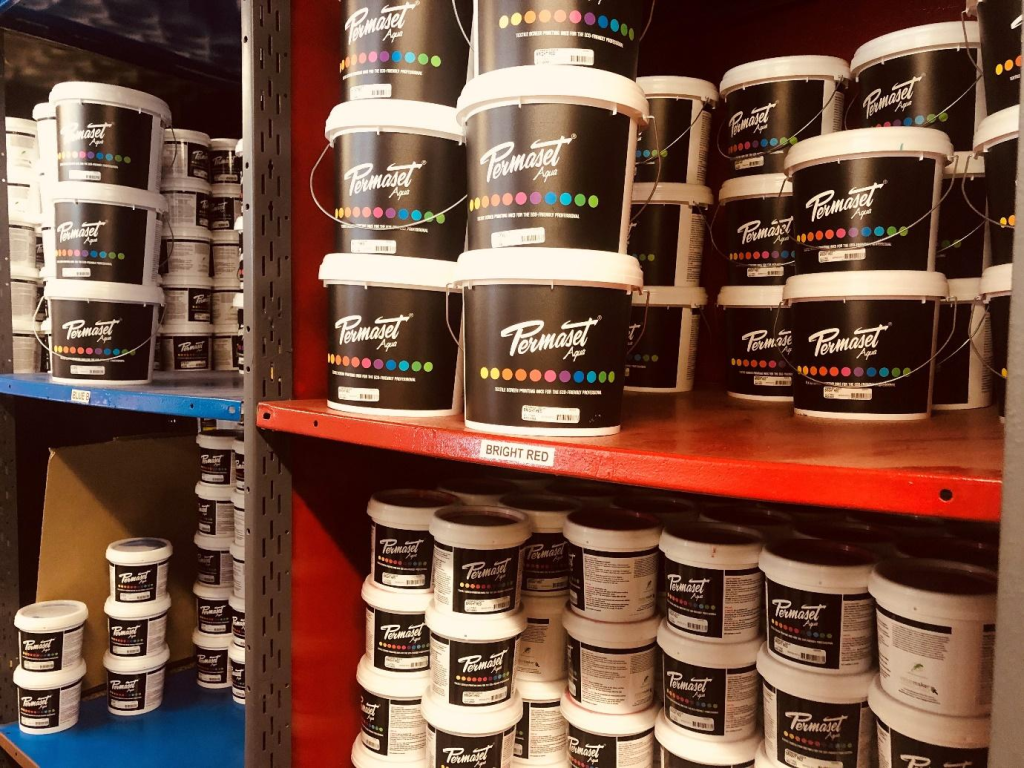
Looking for something softer? Go with water-based ink. It soaks into the fabric, creating a smooth, natural finish that feels breathable – ideal for lighter fabrics like cotton. The key is to match your ink to the vibe you want.
Choose The Right Material
Choosing the right material is just as important as the ink you print since different materials work better with different inks and designs. The texture, absorbency, and durability of the fabric will influence how the ink adheres and how your final print appears.
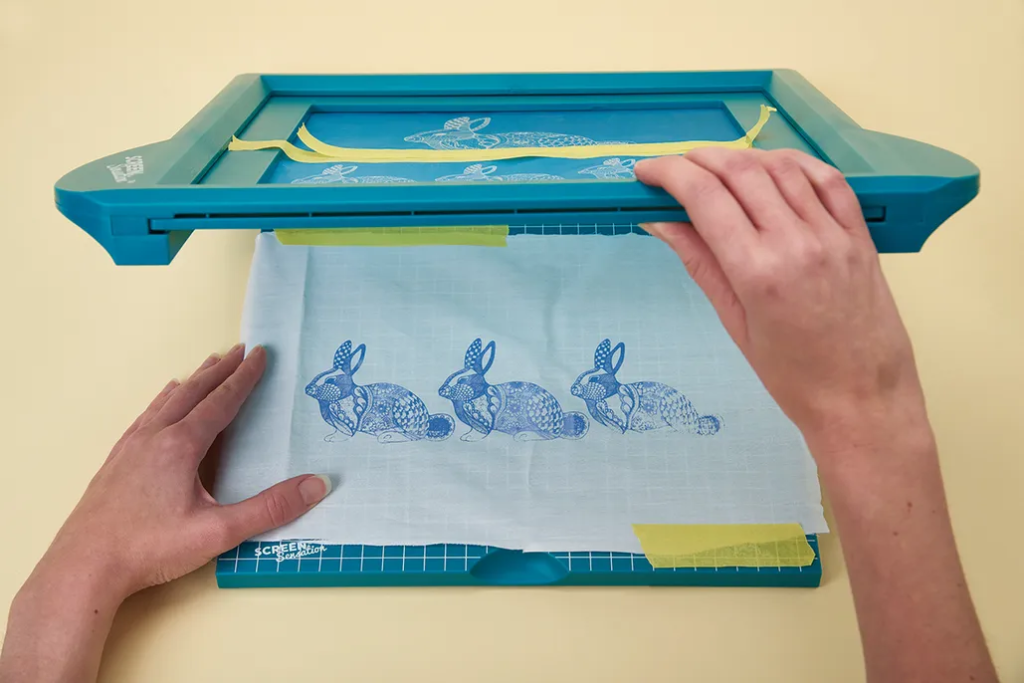
For most projects, you can’t go wrong with cotton. It’s smooth, absorbs ink beautifully, and holds vibrant designs that last through multiple washes.
Need something durable? Polyester is great for sportswear, thanks to its moisture-wicking properties, but it works best with special inks and higher heat settings.
Want a unique twist? Try linen for a rustic, vintage look or canvas for sturdy items like tote bags and banners. Matching your fabric to your design and ink is the secret sauce for success.
Optimize Design
Here’s a tip: simplicity is your friend when it comes to screen printing. While it’s tempting to go for intricate details, overly complicated designs don’t always translate well onto fabric.
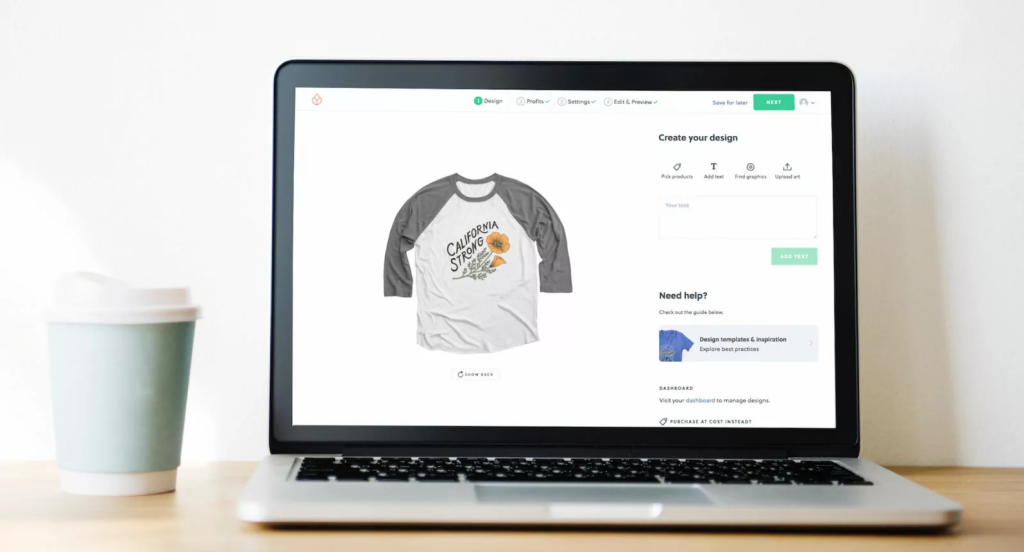
You need to remember to stick to bold lines, clean shapes, and fewer colors to deliver the best results. Yet, if your design has multiple colors, remember that each one needs its own screen layer. This process, called color separation, ensures each color is crisp and vibrant.
Regular Maintenance
There is one last aspect you don’t want to overlook: proper maintenance of your screen printing equipment to make sure your prints stay sharp and your setup runs smoothly.
Think of your tools as the backbone of your prints—keep them in top shape.
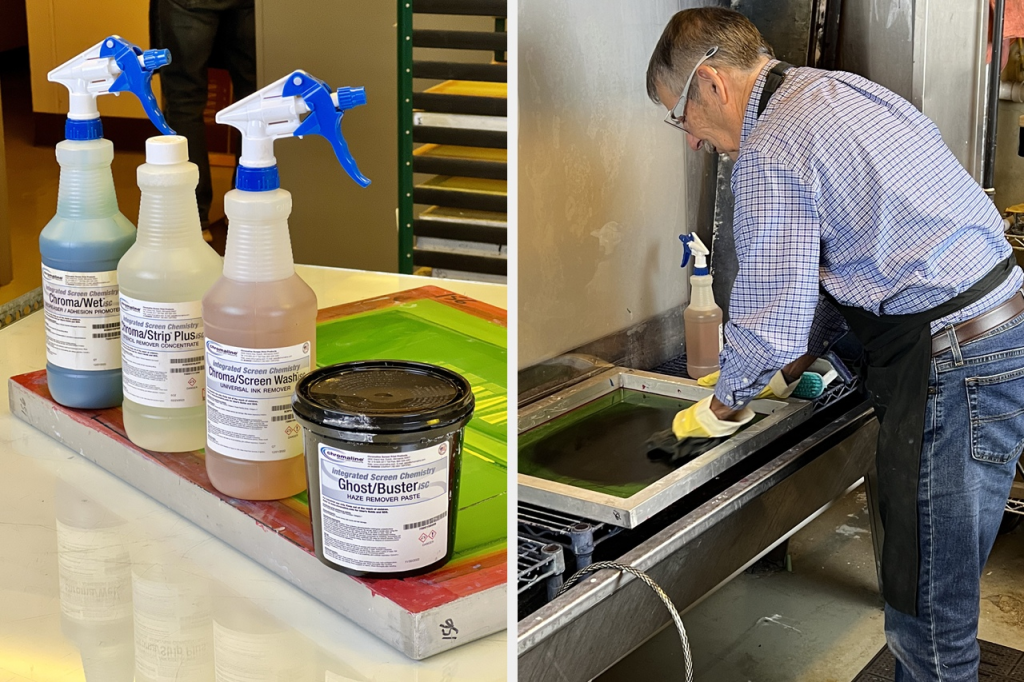
After every use, clean your screens thoroughly to prevent ink buildup, which can mess with your prints. Check the tension on your mesh screens regularly since uneven tension can lead to blurry designs.
And don’t forget your squeegees! Worn-out ones can ruin the even spread of ink, so replace them when needed.
Screen Printing Compared to Other Printing Methods
Here’s a quick comparison of screen printing with other popular methods (DTG Printing and Heat Transfer Printing) to help you choose the right one for your project:
Printing Method | Screen Printing | DTG Printing | Heat Transfer Printing |
---|---|---|---|
Best For | Bulk printing, textiles | Small runs, detailed designs | Custom orders, fabrics |
Setup Cost | High (screen creation) | Low (no setup needed) | Low (requires transfer sheets) |
Cost per Unit | Low (for large orders) | High (for large runs) | Moderate (depends on materials) |
Detail | Limited (best for bold designs) | High (ideal for detailed artwork) | Moderate (depends on design) |
Material Compatibility | Fabrics, various materials | Best on cotton | Works on most fabrics |
Durability | High (long-lasting prints) | Lower (less durable) | Moderate (may fade or peel) |
Speed | Fast (after setup) | Slow (for large orders) | Fast (for small runs) |
Conclusion
Above, I gave you a detailed look into what is screen printing and how it works. While this method is perfect for large projects and vibrant designs, it has some limitations, especially for intricate details. With the right materials and techniques, though, screen printing can deliver durable, high-quality prints for various applications.